Nový přístup k výsledkům vnitřní inspekce
Kombinace materiálových zkoušek, korozního průzkumu, vnitřní inspekce, odstranění zásadních nalezených vad a následného testu integrity je nejefektivnější způsob, jak prokázat spolehlivost dlouhodobě provozovaných vysokotlakých potrubí a zajistit jejich budoucí bezpečný provoz.
V šedesátých letech minulého století byl na území Sovětského svazu vybudován ropovod DN 700 Polock–Ventspils, který sloužil k přepravě ruské vývozní ropy do terminálu u přístavního města Ventspils na pobřeží Baltického moře – viz obrázek 1. Z tohoto přístavu ležícího na území Lotyšska exportoval Sovětský svaz v druhé polovině minulého století ropu do celého světa.
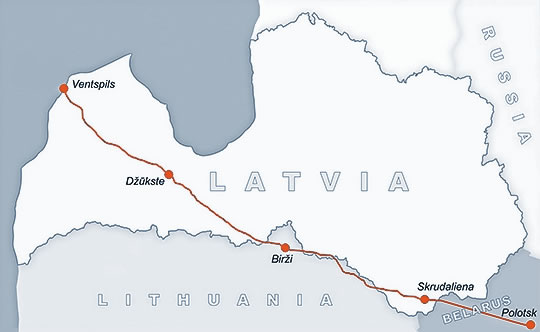
Obrázek 1 – Trasa ropovodu Polock–Ventspils
Přibližně před 12 lety došlo k zastavení provozu tohoto ropovodu z důvodu omezení dodávek ropy z Ruska. Nastala tak situace, kdy bylo potrubí ropovodu téměř 10 let v celém objemu zaplněno stojící ropou. Zastavení provozu provozovatele samozřejmě nezbavuje povinností provádět na potrubí pravidelnou údržbu zajišťující bezpečnost a funkčnost ropovodu. Proto bylo v letech 2010–2013 společností CEPS vyprázdněno, chemicky vyčištěno a zakonzervováno 250 km potrubí v úseku od lotyšsko-litevské hranice po Ventspils.
Na podzim 2012 bylo vedením společnosti SIA LatRosTrans (vlastníka potrubí) rozhodnuto prověřit možnost revalidace (komplexního ověření integrity) tohoto vysokotlakého potrubí za účelem jeho budoucího využití.
K posouzení byl vybrán cca 8 km dlouhý úsek již chemicky vyčištěného potrubí mezi 379. kilometrem a čerpací stanicí Džūkste. Provedená revalidace zahrnovala tyto základní kroky:
- materiálové zkoušky vzorků z potrubí a modelová zkouška testu integrity trubního tělesa,
- analýzu výsledků materiálových zkoušek,
- off-line inspekci pomocí TFI-ježka řízeně protlačeného potrubím pomocí vody,
- analýzu výsledku vnitřní inspekce,
- vypracování programu nutných oprav a testu integrity,
- realizaci programu oprav,
- test integrity,
- sušení,
- inertizaci.
Všechny tyto činnosti proběhly v průběhu roku 2013. Generálním dodavatelem těchto prací byl CEPS, veškeré svařečsko-montážní a zemní práce zajistila SIA LatRosTrans.
Technické parametry potrubí
Potrubí ropovodu bylo postaveno koncem šedesátých let minulého století. K použitému trubnímu materiálu se bohužel nedochovaly z doby výstavby žádné dokumenty kontroly. Dle informací od provozovatele se jedná o podélně svařované potrubí 720 × 7 až 10,2 mm vyrobené dle GOST 10704-63 (standard pro výrobu podélně svařovaných trubek) z oceli 17GS dle GOST 5058-65 (standard pro výrobu plechů z uhlíkové oceli válcovaných za tepla).
Ropovod byl projektován na maximální tlak 64 bar. Před uvedením do provozu byla na potrubí v roce 1968 provedena hydraulická tlaková zkouška tlakem 60 bar, v roce 1990 se uskutečnila opakovaná tlaková zkouška tlakem 56 bar.
Pro provedení revalidace byla vybrána část ropovodu mezi osadou Peteri (cca 379. km trasy) a čerpací stanicí Džūkste v délce cca 8 km. Nadmořská výška terénu v trase potrubí se pohybovala v intervalu 34 až 61 m nad mořem. Potrubí je v celé své délce průchozí pro čistící i inteligentní ježky.
Materiálové zkoušky a modelová zkouška trubního tělesa
Z trasy ropovodu DN 700 v úseku 379. km – Džūkste byl vyříznut trubní vzorek o délce 8 m, který byl tvořen dvěma podélně svařovanými trubkami spojenými montážním obvodovým svarem. Z tohoto svařence byly odříznuty tři vzorky v délce 3 × 1 m pro materiálové zkoušky. Ze zbylé cca 5 m dlouhé části trubního vzorku bylo zhotoveno zkušební tlakové těleso určené k modelovému testu integrity, následnému cyklování a tlakování k mezi pevnosti – tedy do destrukce.
Základní chemické složení, mechanické a metalografické vlastnosti trubního materiálu byly experimentálně stanoveny ve společnosti SVÚM, a. s. Lomově-mechanickou analýzu trubního materiálu včetně zkoušky kinetiky růstu únavové trhliny a stanovení prahového a kritického rozměru trhliny se uskutečnily ve zkušebnách CEPS a Ústavu teoretické a aplikované mechaniky Akademie věd České republiky, v. v. i.
Modelový test integrity, cyklování a tlakování do destrukce zkušebního tlakového tělesa byly provedeny opět ve zkušebně CEPS ve spolupráci se společností ADA Akustická emise, s. r. o., která zajistila při prováděných hydraulických zkouškách měření systémem akustické emise (AE).
Materiálové zkoušky
Podle původního standardu GOST 5058-65 a i později vydaného standardu GOST 5520-79 musí vlastnosti oceli 17GS splňovat minimálně parametry uvedené v tabulce 1.
Re [MPa] | Rm [MPa] | A [%] | KCV při 0 °C [J/cm²] | KCU při –40°C [J/cm²] |
---|---|---|---|---|
min. 345 MPa | min. 510 MPa | min. 23 % | min. 34 | min. 44 |
Podle výsledků uskutečněných zkoušek materiál dodané trubky svými vlastnostmi vyhovuje požadavkům těchto ruských standardů, kromě požadavku na vrubovou houževnatost při −40 °C – viz tabulka 2. V reálné praxi se však u podzemních vedení takto extrémních teplot běžně nedosahuje ani v podmínkách lotyšské zimy. Z tohoto důvodu se hodnota vrubové houževnatosti při záporných teplotách pro ocelová potrubí dodávané dle ČSN EN ISO 3183 ani podle dříve platné ČSN EN 10 208-2 standardně neudává, resp. nevyžaduje.
Místo odběru vzorku, orientace | Rp0,2 [MPa] | Rt0,5 [MPa] | Rm [MPa] | A [%] | Z [%] | KCV při 0 °C [J/cm²] | KCV při –40°C [J/cm²] |
---|---|---|---|---|---|---|---|
Obvodový směr | 375 | 417 | 561 | 26,60 | 50,64 | 56 | 17 |
Podélný směr | 373 | 389 | 560 | 28,07 | 56,82 | 79 | 18 |
Svarový kov | – | – | – | – | – | 52 | 25 |
Tepelně ovlivněná zóna | – | – | – | – | – | 64 | 17 |
Následně provedené lomově-mechanické zkoušky pak prokázaly, že základní materiál potrubí má dobrou schopnost otupit a zablokovat ostré vady typu trhlin.
Příprava zkušebního tělesa, rozsah zkoušek
Z hlavní části trubního vzorku bylo zhotoveno zkušební tlakové těleso, na kterém byly postupně provedeny následující zkoušky a měření:
- nedestruktivní defektoskopie (NDT) svarů,
- orientační měření tloušťky stěny potrubí a tvrdosti,
- modelový test integrity,
- cyklické tlakové zkoušky pro ověření únavové odolnosti,
- tlakování do destrukce.
Návarky na zkušebním tělese byly osazeny armaturami, na které se napojily vysokotlaké hadice pro přívod a odpouštění tlakové vody a elektronické snímače tlaku. Na trubní těleso byly poté připevněny senzory akustické emise (AE) – viz obrázek 2.
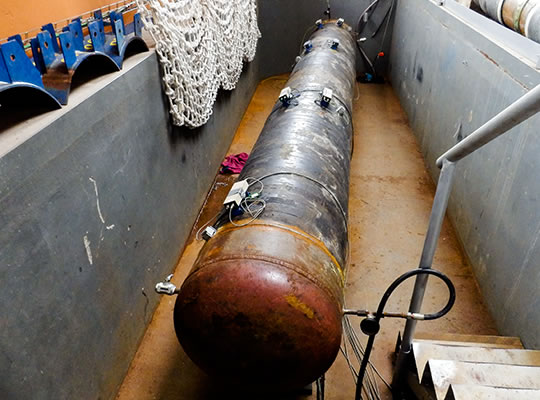
Obrázek 2 – Zkušební těleso
Modelový test integrity zkušebního tělesa
Modelový test integrity, tedy řízené tlakové přetížení trubního tělesa k hranici meze kluzu, byl proveden podle pracovního postupu CEPS 98 Test integrity potrubí včetně stabilizace vad. Tento test integrity je speciálně modifikovaný stresstest, který vychází z českého technického standardu TPG 702 04 a německého standardu VdTÜV – Merkblatt 1060, při kterém je tlakem vody v potrubí vyvoláno ve stěně trubky napětí blížící se integrální mezi kluzu. Určení hodnoty tohoto tlaku je jedna z nejdůležitějších částí přípravných prací, neboť:
- při nízkém tlaku by se příznivé účinky testu integrity vůbec neprojevily,
- při vysokém tlaku by došlo k negativnímu ovlivnění materiálu a zhoršení stavu potrubí i izolace.
Parametry tohoto modelového testu integrity byly stanoveny na základě výsledků provedených materiálových zkoušek. Veškeré tlakování probíhalo za kontinuálního měření AE. Snímače AE byly osazeny v rozmístění pro plošnou lokalizaci, což umožňovalo přesné určení polohy zdrojů akustických událostí, tedy míst rozvoje mikrodefektů v trubním tělese. V průběhu modelového testu integrity se pomocí měřicích citlivých přístrojů s vysokou přesností a počítačů on-line měřil, vyhodnocoval a automaticky zaznamenával:
- tlak ve zkušebním tělese,
- průtok přičerpávané vody,
- závislost p–V (závislost tlaku na přičerpaném objemu vody),
- závislost nárůstu tlaku na přičerpávaném objemu vody ΔV/Δp,
- závislost p–t (záznam tlaku v čase),
- hodnota přičerpaného objemu vody pro plasticku deformaci ΔVplast.,
- hodnota integrální obvodové plastické deformace ε,
- chování mikroobjemů materiálů pomocí akustické emise, která reaguje na rozvoj mikrodefektů materiálů.
V průběhu testu integrity bylo akustickou emisí zaznamenáno 13 emisních událostí. Převážná většina z nich byla zaznamenána pouze v 1. cyklu testu integrity. Akustická emise se tedy projevila standardním Kaiserovým efektem, což svědčí o odbourání vnitřních pnutí a stabilizaci vad v materiálu potrubí.
Cyklické zkoušky zkušebního tělesa
Po provedeném testu integrity byla ověřena odolnost trubky vůči únavovému rozvoji vad typu trhlin, čímž se ověřuje doba, o kterou lze testem integrity prodloužit životnost potrubí. Zkušební těleso bylo podrobeno únavovému cyklickému zatěžování při rozmezí tlaku cca 9,3 až 56,7 bar.
V průběhu cyklického zatěžování se pomocí měřících přístrojů a počítačů on-line měřil, vyhodnocoval a automaticky zaznamenával:
- tlak ve zkušebním tělese,
- záznam tlaku v čase (kontrola počtu a velikosti zkušebních tlakových cyklů) – viz obrázek 3,
- vývoj signálu akustické emise během zkoušek (kontrola vzniku možného rozvoje trhlin únavovým mechanizmem).
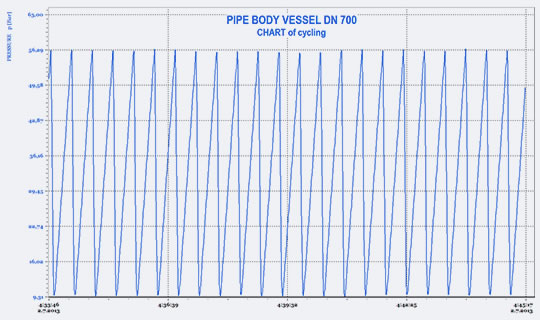
Obrázek 3 – Část záznamu tlaku v čase při cyklických zkouškách
V průběhu 7 dní bylo na zkušebním tělese provedeno 16 194 cyklů, což při frekvenci 1 cyklus/den simuluje více než 40 let dalšího života potrubí. Při cyklickém zatěžování zkušebního tělesa nebyl nalezen žádný zdroj akustické emise vykazující znaky rozvoje únavového poškození materiálu. Provedené cyklické zkoušky uskutečněné po modelovém testu integrity plně prověřily zvýšenou odolnost trubního vzorku proti možnému únavovému rozvoji vad.
Tlakování do destrukce
Tlakování do destrukce probíhalo monotónním zatěžováním bez prodlev. Destrukce trubního materiálu zkušebního tělesa nastala při tlaku 101,45 bar. Tento tlak byl o cca 1,5 bar nižší, než by odpovídalo teoretickému tlaku na mezi pevnosti. Příčinou destrukce bylo porušení integrity trubního materiálu v přechodové oblasti podélného továrního svaru, odkud se vzniklá trhlina rozšířila v ose potrubí oběma směry a zastavila se až po vybočení do základního trubního materiálu – viz obrázek 4.
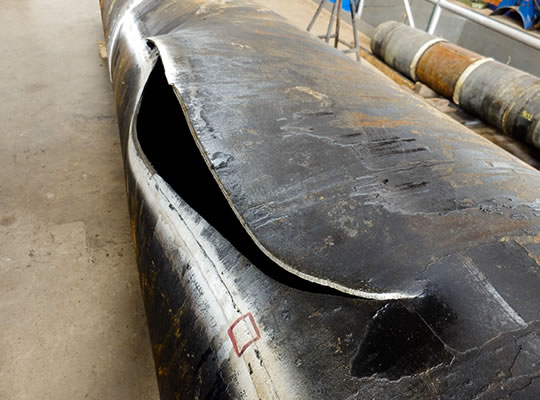
Obrázek 4 – Zkušební těleso DN 700 po destrukci
Zhodnocení materiálových a modelových zkoušek
Provedené materiálové zkoušky prokázaly vysokou kvalitu ocelového materiálu potrubí ropovodu a jeho vlastnosti (kromě již diskutovaného nedodržení normové hodnoty vrubové houževnatosti při −40 °C) s rezervou splňují požadavky dle standardu GOST 5520-79 a po více než čtyřicetileté době provozu nebyly zjištěny žádné známky degradace trubního materiálu.
Z výsledků testu integrity a z měření akustickou emisí vyplynulo, že v průběhu řízeného tlakového přetížení trubního vzorku k hranici meze kluzu došlo ke snížení vnitřních pnutí a stabilizaci vad v materiálu potrubí.
Následně v průběhu cyklických zkoušek nebyl v trubním vzorku akustickou emisí detekován žádný rozvoj nebezpečných vad, a to ani při velmi drastické simulaci dlouhodobého provozu cyklickým zatěžováním vnitřním přetlakem. Na základě výsledků experimentálního vyšetřování vlastností materiálu potrubí a jejich analýzy bylo možné konstatovat, že potrubí je vhodné pro provedení testu integrity a jako takové má reálné předpoklady, že po jeho uskutečnění jej bude možné bezpečně a spolehlivě provozovat jako plynovod nebo produktovod.
Vnitřní inspekce potrubí
Jak je všeobecně známo, na potrubích se téměř vždy vyskytují výrobní vady, které výstupní kontrolou zachyceny nebyly, dále vady z montáže potrubí (svařování, pokládka), vady iniciované provozním zatížením, korozní vady nebo vady způsobené třetí stranou. Z tohoto důvodu byla na vybraném úseku potrubí provedena vnitřní inspekce, jejíž hlavním cílem bylo detekovat a lokalizovat vady, které by zcela jistě tlak při následném testu integrity nevydržely.
Na potrubí ropovodu DN 700 Polock–Ventspils naposledy proběhla vnitřní inspekce pomocí MFL- a UT-ježka roce 2000. Krátce po provedené inspekci bylo čerpání ropy ropovodem zastaveno a tlak v potrubí snížen na minimum, resp. závisel pouze na hydraulickém tlaku a teplotě ropy. V tomto provozním režimu se již nepředpokládal další rozvoj únavových vad (především vznik a růst trhlin ve stěně potrubí) způsobený střídáním tlaků v ropovodu. I přes nepřetržitou funkci katodové ochrany však nebylo možné v průběhu těchto posledních 13 let vyloučit nárůst defektů způsobených korozí.
Z uvedeného důvodu rozhodl vlastník potrubí uskutečnit před provedením testu integrity vnitřní off-line inspekci pomocí TFI-ježka. Inspektovaný úsek potrubí nebyl vybaven komorami pro vkládání a přijímání ani inteligentních ani čistících ježků. Z tohoto důvodu CEPS v předstihu zabezpečil navržení a výrobu dočasných komor a mobilních nástavců pro provedení zatím ne příliš běžné inspekce v režimu off-line – viz obrázek 5.
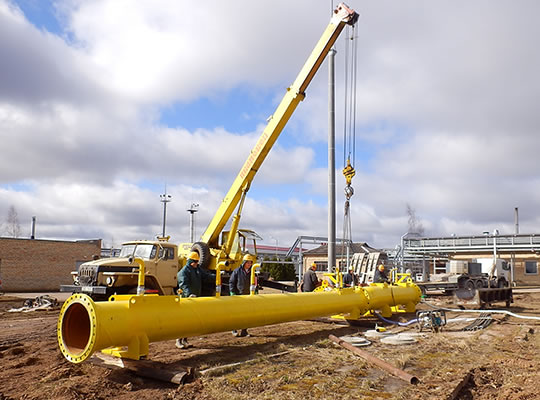
Obrázek 5 – Mobilní nástavce pro inspekční ježky
Jelikož potrubí ropovodu zůstalo po chemickém vyčištění a následné konzervaci prázdné, bylo nutné zajistit rovnoměrný posun ježka potrubím náhradním mediem. V tomto případě byla jako náhradní medium použita voda, která se v dostatečném množství nacházela v areálu čerpací stanice. Protlačení TFI-ježka potrubím pomocí čerpané vody zajistil CEPS ve spolupráci s LatRosTrans.
Pohon inspekčního ježka
Řízené protlačení TFI-ježka potrubím se uskutečnilo pomocí vody, která byla čerpána z dočasných nádrží v areálu čerpací stanice v Džūkste. Na základě požadavků dodavatele vnitřní inspekce musel být TFI-ježek protlačen potrubím rychlostí alespoň 0,5 m/s – viz obrázek 6, což odpovídá rychlosti čerpání minimálně cca 190 l/s, resp. cca 685 m³/h vody do potrubí. Celkem bylo za cca 4,5 hodiny načerpáno 3 100 m³ vody, což odpovídá celkovému geometrickému objemu potrubí.
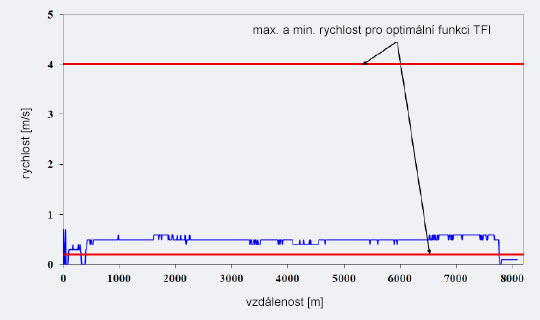
Obrázek 6 – Rychlost pohybu TFI-ježka potrubím
Po protlačení TFI-ježka potrubím byla použitá voda vytlačena z potrubí a přepuštěna zpět do rezervoárů. Pro ilustraci – toto množství vody by stačilo napájet všechny fontány v zahradách ve Versailles po dobu celé jedné hodiny.
Pro zajištění dodávky tohoto obrovského množství vody v průběhu několika hodin, bylo nutné mezi rezervoáry a koncem potrubí DN 700 postavit čtyři dočasné vodovody (1× DN 200 a 3× DN 100), které propojily mobilní čerpadla umístěná u rezervoárů s koncem potrubí inspektovaného úseku – viz obrázek 7.
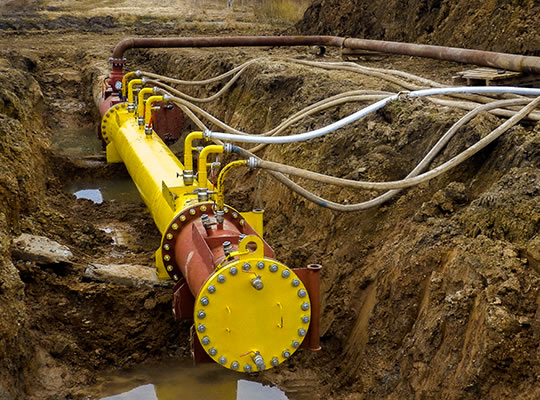
Obrázek 7 – Napojení sestavy vysílací komory a nástavců na vodovodní potrubí
Po vyjmutí inspekčního ježka z přijímacího nástavce byla provedena kontrola naměřených dat. Tato kontrola potvrdila, že TFI-ježek byl při již při svém prvním běhu protlačen potrubím požadovanou rychlostí a naměřená data jsou použitelná pro jejich další zpracování.
Analýza výsledků diagnostického průzkumu
Po provedení vnitřní inspekce byla provedena analýza naměřených dat. Seznam vad doporučených k opravě na základě provedené analýzy dat vždy vychází z požadavku zajištění budoucího bezpečného provozu dálkovodu. Při vnitřní inspekci jsou ve stěně potrubí zaznamenány anomálie, které jsou následně zkoumány a hodnoceny.
Na základě know-how dodavatele a typu použitého inspekčního ježka jsou detekované anomálie vyhodnocovány jako vady určitého typu a velikosti. Tyto vady jsou následně podle různých analytických metod hodnoceny z pevnostního hlediska. Při těchto výpočtech je nedostatek informací o skutečném tvaru a rozměru každé vady vždy korigován pomocí mnoha faktorů. Na základě následných pevnostních výpočtů a nastavených kritérií jsou pak doporučeny k opravě vady, které teoreticky nesplňují nastavené pevnostní požadavky.
Množství vad doporučených k opravě vždy závisí na druhu použité hodnotící analytické metody. Pevnostní výpočty všech defektů byly počítány pro tlak 32,6 bar, což byl maximální tlak, na kterém byl ropovod v minulosti provozován.
Na základě provedené analýzy doporučil dodavatel vnitřní inspekce uskutečnit do 1 roku 11 oprav, do 2 let 1 opravu, v horizontu 10 let 22 oprav a další desítky vad při generální opravě.
V prvním roce byly doporučeny k opravě především promáčkliny, které by mohly potenciálně obsahovat další defekt, v horizontu deseti let pak (kromě promáčklin) i některé korozní vady.
Podstata testu integrity
Test integrity je speciálně modifikovaný stresstest dlouhodobě provozovaných ocelových potrubí, který prověří skutečnou integrální mez kluzu potrubí a tedy jeho bezpečnost vůči provoznímu tlaku. Principem tohoto testu je zatížení zkoušeného potrubí vysokým tlakem vody až na úroveň blízkou integrální mezi kluzu, resp. ve stěně trubky je přetlakem vody vyvozeno napětí blížící se mezi kluzu.
Lokální místa s vnitřním pnutím projdou během testu integrity plastickým stavem se zpevněním materiálu, který se při dalším zatěžování chová již jako pružný. Dochází samozřejmě k odčerpání určité části plastické rezervy materiálu, toto odčerpání je ovšem minimální a při testu integrity je s ním počítáno.
Při testu integrity dochází k příznivému ovlivnění následujících charakteristik potrubí a jeho materiálu:
- snížení a přerozdělení vnitřních pnutí (napětí) vzniklých ve stěně trubky při jejich výrobě,
- snížení a přerozdělení napětí vzniklých pokládkou potrubí,
- přerozdělení špiček napětí v místě koncentrátorů napětí–vrubů (vad),
- snížení špiček napětí ve větších oblastech stěny (např. svar a jeho přechodová zóna, ovalita, deformace) a eliminace vzniku trhlin koroze pod napětím a rozvoje únavových trhlin,
- redistribuce nepříznivých koncentrátorů napětí u vad typu plošných nebo důlkových korozních napadení,
- zablokování rozvoje podkritických avšak růstuschopných ostrých vad (typu trhlin) vytvořením plastické zóny na jejich čele a vznikem tlakových napětí v této zóně po odlehčení,
- částečné zablokování růstu trhlin podkritické velikosti charakteru koroze pod napětím, jež jsou jinak problematicky dohledatelné,
- otevření nadkritických vad. Vzhledem k tomu, že se tlak vyvozuje vodou, je otevření bezpečné, a místo s poruchou se vyhledá, odhalí a nahradí novou trubkou.
Výsledkem provedeného testu integrity se tak kromě ověření současného technického stavu potrubí vytvoří především podmínky pro jeho další bezpečný provoz odstraněním zjevných závad na potrubí a dlouhodobým zablokováním (stabilizací) dalšího rozvoje ostatních vad ve stěně potrubí únavovými procesy.
Přehodnocení vad a doporučení z vnitřní inspekce vzhledem k následnému ověření integrity potrubí
V rámci revalidace potrubí byla cíleně použita kombinace vnitřní inspekce a následného testu integrity tlakovým přetížením. To umožňuje zásadně odlišný přístup k výsledkům vnitřní inspekce. Vady z inspekce se rozdělí do dvou základních skupin:
- vady velké (nadkritické), které by se při testu integrity zcela jistě otevřely. Tyto vady se opraví výřezem,
- vady menší (podkritické), které by sice při samotné vnitřní inspekci musely být opraveny, ale při tlakovém přetížení v rámci testu integrity budou stabilizovány, takže jejich oprava není nutná.
Tento přístup významným způsobem snižuje potřebný počet oprav potrubí po jejich inspekci a přináší podstatně vyšší výslednou spolehlivost potrubí, protože při testu integrity se stabilizují i další vady, které nebyly v rámci inspekce doporučeny k opravě, nebo dokonce nebyly detekovány vůbec. Takové nedostatečně detekované nebo ohodnocené vady se dokonce při testu integrity mohou projevit jako nadkritické a otevřít se.
Při přehodnocení vad detekovaných a standardně vyhodnocených dodavatelem vnitřní inspekce byl zvolen následující přístup:
- Vady typu promáčklin, laminací a svarových defektů nebyly opravovány – pevnost potrubí byla v tomto místě prověřena při testu integrity. Předpokládalo se, že v průběhu testu integrity dojde v těchto místech k přerozdělení špiček napětí v místě koncentrátorů napětí-vrubů. Tato teorie byla ověřena např. již při modelovém testu integrity zkušebního tělesa, kdy obvodový svar byl vyhodnocen jako nevyhovující z důvodu chybějící kořenové vrstvy. Při provedeném testu integrity však došlo k stabilizaci těchto vad v kořenové oblasti obvodového svaru, což potvrdily signály AE. Navíc destrukce trubního tělesa nastala v tepelně ovlivněné zóně podélného svaru, kde žádný defekt nalezen nebyl.
- Vady typu úbytku materiálu byly přepočítány podle analytických metod:
- B31.G (ASME),
- B31.G modifikované (ASME) a RSTRENG,
- DNV – Code.
- Hodnotícím kritériem pro každou vadu tohoto typu bylo, zda vyhovuje z pevnostního hlediska zatížení při předpokládaném max. tlaku při testu integrity (v tomto případě se jednalo o hodnotu 75 bar).
- Vady typu nežádoucích konstrukčních prvků nebo vady provizorně opravené za provozu byly vždy navrženy k opravě. Týkalo se provizorních oprav (zaslepení) černých navrtávek, záplat a odstranění odvzdušňovacího potrubí.
Pokud by se hodnotily výše uvedené metody z hlediska konzervativnosti, je všeobecně známo, že kritérium B31.G je spolehlivé, avšak v praxi značně konzervativní. Pro snížení stupně konzervativnosti byly následně vyvinuty a odzkoušeny kritéria B31.G modifikované a RSTRENG. Kritérium DNV – Code (RP-F 101) je vůči metodě B31.G méně konzervativní vzhledem ke všem rozměrům plošného poškození.
Jako základ pro výběr vad s úbytkem materiálu určených k opravě bylo zvoleno hodnocení vad metodou B31.G modifikované a RSTRENG s přihlédnutím k hodnocení vad pomocí metody DNV – Code. Všechny vady, u kterých by bylo při testu integrity dosaženo teoretického (výpočtového) maximálního zatížení, resp. destrukce, byly určeny k opravě. Všechny svařečsko-montážní, zemní a izolatérské práce, které byly realizovány podle takto definovaného „programu oprav“, provedl LatRosTrans.
Způsob oprav vad
Na rozdíl od všech předchozích oprav, které se na ropovodu uskutečnily v minulosti, byly nyní díky provedené inertizaci potrubí veškeré svářečsko-montážní práce (svařování, broušení a řezání plamenem) prováděny v již trvale bezpečné atmosféře, bez jakýchkoliv jinak nutných bezpečnostních opatření pro zajištění nevýbušné atmosféry. Z uvedeného důvodu nebyly instalovány žádné objímky nebo záplaty, ale potrubí bylo v těchto místech vyříznuto v délce min. 1 m a propojeno trubkou.
Malé vady typu provizorně opravených černých navrtávek byly překryty návarky TDW TOR 2 in., PN 100. Následně byla navrtávacím zařízením TDW stěna potrubí provrtána. Tím došlo k odstranění případných vrubů ve stěně potrubí a zároveň se zajistilo, že prostor návarku bylo možné po provedeném testu integrity nejenom vypustit, ale i vysušit.
Destrukce v průběhu testu integrity
Před provedením hydraulických zkoušek bylo potrubí ropovodu rozděleno přibližně v polovině na dva úseky. V průběhu řízeného zvyšování tlaku došlo na úseku 1 při tlaku 70,5 bar k destrukci potrubí. Při této destrukci poklesl tlak v potrubí během 1 sekundy na 0 bar, což odpovídalo úniku cca 10 m³ vody. Na základě této skutečnosti se předpokládalo, že místo destrukce bude možné nalézt pochůzkou po trase. Tento předpoklad se plně potvrdil, protože místo destrukce bylo lokalizováno během jedné hodiny. Jak je patrné z obrázku 8, nebyl tento mohutný únik vody až tak devastující pro své okolí, nicméně zabezpečení trasy proti pohybu osob a techniky po dobu tlakových zkoušek je nezbytností.
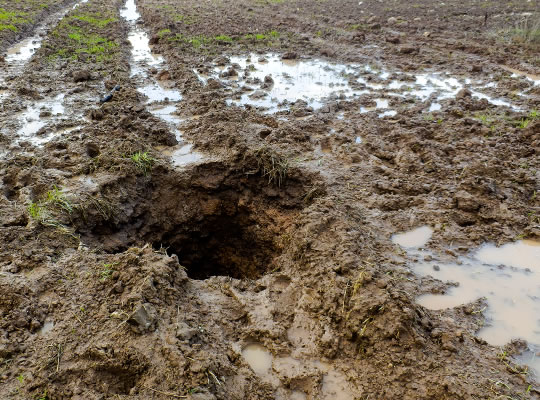
Obrázek 8 – Místo destrukce
Příčinou destrukce byla podélná trhlina uprostřed podélného továrního svaru na vnější straně potrubí v poloze 12 – viz obrázek 9. Příčné (obvodové) řezy na potrubí byly provedeny až následně při svářečsko-montážních pracích spojených s provizorní opravou poškozeného místa, neboť z úseku muselo být před definitivní opravou vytěsněno cca 1 700 m³ vody.
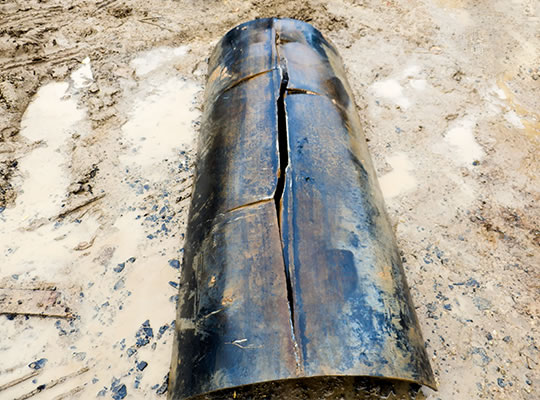
Obrázek 9 – Potrubí poškozené destrukcí
U porušeného podélného továrního svaru byla při vnějším povrchu lomová plocha pokryta černým povlakem – viz obrázek 10. Tento povlak v nejhlubším místě zasahoval, až do hloubky 7 mm, přičemž celková tloušťka stěny trubky v místě defektu, tedy oblast podélného svaru, byla cca 11 mm. Tato oblast při vnějším povrchu s nesouvisle černým povlakem byla cca 150 mm dlouhá, avšak celková délka trhliny dosahovala délky až 250 mm.
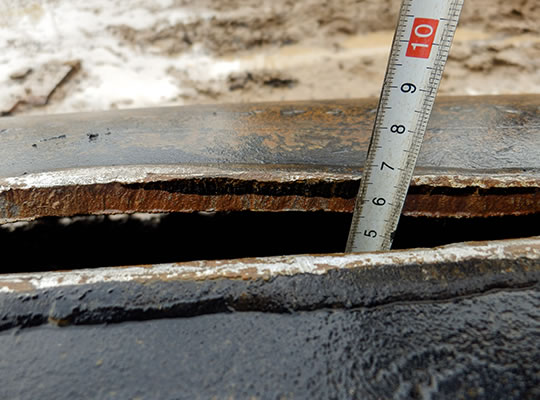
Obrázek 10 – Stěna potrubí v místě destrukce
Šetřením se zjistilo, že černým povlakem na stěně lomové plochy byl standardně používaný asfaltový izolační primer. Při nanášení tovární izolace pravděpodobně pronikla použitá rozehřátá asfaltová hmota částečně do povrchové trhliny podélného svaru. Stupeň pokrytí povrchu trhliny nátěrovou hmotou samozřejmě závisel na jejím rozevření. To vysvětluje, proč nebyla povrchová trhlina kontaminovaná asfaltem v celé své délce. Z uvedeného zjištění jasně vyplynulo, že tato podélná trhlina musela vzniknout již v procesu výroby, existovala v potrubí více než 40 let a zůstala skryta všem běžně dostupným metodám vnitřní inspekce, které byly v průběhu posledních 13 let nasazeny.
Tento případ opět potvrdil dlouholeté zkušenosti CEPS, že i velice nebezpečné vady těchto rozměrů, a to především trhliny v podélném směru potrubí, jsou inteligentními ježky v současné době velice těžko detekovatelné.
Zde je důležité poukázat i na skutečnost, že defekty, které byly po standardním vyhodnocení vnitřní inspekce doporučeny k opravám, ale po provedených pevnostních výpočtech opravovány nebyly, vydržely tlak 72 bar po dobu 24 hodin, tedy cca dvojnásobný tlak, než na který byl proveden původní výpočet dodavatelem TFI. Naopak k destrukci podélného svaru došlo v místě, kde ani TFI, ale ani Ultrasonic a MFL v roce 2001 nic významného nedetekovaly, ačkoliv trhlina uvedené velikosti ve svaru při inspekcích již prokazatelně existovala. Po provedené opravě byl test integrity na úseku 1 zopakován. Na základě provedeného testu integrity (stresstest, test pevnosti a těsnosti) bylo potrubí úseku 1 prohlášeno za pevné a těsné. Následně byly hydraulické zkoušky stejným způsobem provedeny i na druhém úseku, který byl rovněž vyhodnocen jako pevný a těsný.
Po provedených hydraulických zkouškách bylo potrubí vysušeno na teplotu rosného bodu (TRB) −20 °C a opět natlakováno inertizační dusíkovou směsí.
Polský případ
V roce 2010 prováděl CEPS test integrity v Polsku na vysokotlakém plynovodním potrubí v délce 56 km. Toto potrubí bylo vybudováno v roce 1997 ze šroubovicově svařovaných trub 406 × 6,3 mm z oceli 18G2A. Před hydraulickými zkouškami proběhla na tomto potrubí vnitřní inspekce pomocí MFL ježka. Na základě této vnitřní inspekce byly všechny defekty, které dodavatel vnitřní inspekce vyhodnotil jako kritické, opraveny. V průběhu prvního cyklu testu integrity byl na jednom ze zkušebních úseků zaznamenán značný únik vody.
Po lokalizaci a odkopání místa úniku vody byl v poloze 12 nalezen impozantní montážní obvodový svar – viz obrázek 11, na jehož krycí vrstvě svářeč materiálem rozhodně nešetřil. Kořen v místě perforace byste však hledali marně. Je s podivem, že tento svar, již na první pohled s tak výraznými nedostatky, mohl projít všemi kontrolami, které měly být prováděny při výstavbě.
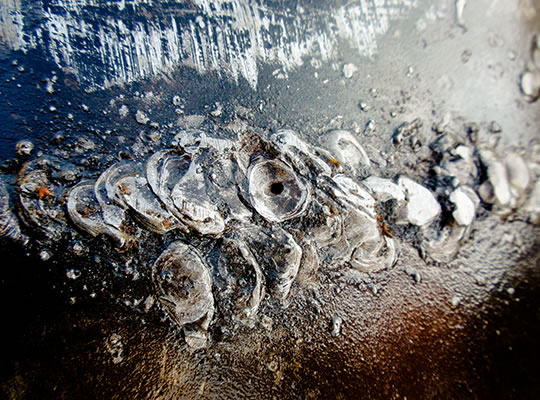
Obrázek 11 – Montážní svar s průchozí vadou
Při zpětné kontrole výsledků vnitřní inspekce tohoto místa nebyly zjištěny v záznamu inteligentního ježka žádné anomálie.
Revalidace produktovodů v ČR
V průběhu posledních 10 let provedl CEPS v ČR testy integrity po vnitřních inspekcích pomocí MFL ježků na více jak 200 km produktovodů. Při těchto zkouškách bylo detekováno více jak 20 vad, které byly průchozí již v průběhu provádění vnitřní inspekce nebo byly příčinou destrukce potrubí v průběhu hydraulických zkoušek. Ve všech těchto případech nejenže nebyly tyto kritické vady doporučeny k opravě, ale dosti často nebyly inteligentním ježkem ani detekovány (viz například obrázek 12).
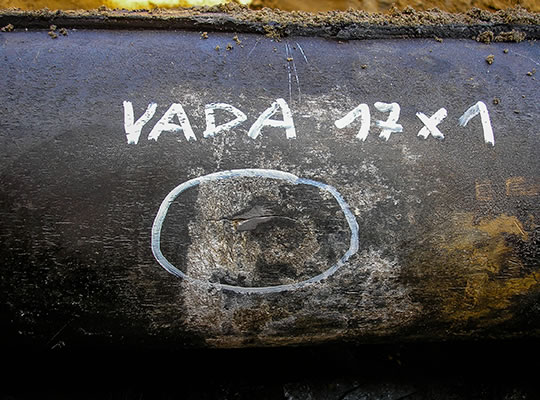
Obrázek 12 – Příklad vady, která nebyla detekována inteligentním ježkem