Новый подход к результатам внутритрубной инспекции
Проходящий по территории Латвии участок выведенного из эксплуатации нефтепровода Ду 700 протяженностью двести пятьдесят километров был опорожнен, химически очищен и законсевирован азотом. Затем, оператор трубопровода рассматривал возможность применения нефтепровода после 45-летней службы для транспортировки других сред. В 2013 году была в данных целях проведена повторная проверка (ревалидация) данной трубы. В рамках данной повторной проверки намеренно применили комбинацию внутритрубной инспекции и последующего испытания на целостность, что позволило принять принципиально иной подход к результатам внутритрубной инспекции.
В шестидесятые годы прошлого века был на территории Советского Союза построен нефтепровод Ду 700 Полоцк–Вентспилс, который служил для транспортировки российской нефти в экспортный терминал вблизи портового города Вентспилс на Балтийском море – см. рис. 1. Во второй половине прошлого века из данного порта, находящегося на территории Латвии, экспортировал Советский Союз нефть в самые разные страны мира.
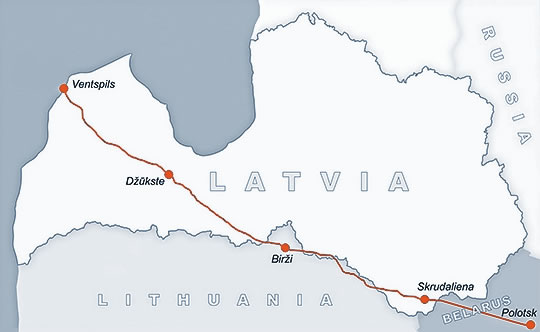
Рис. 1 – Маршрут нефтепровода Полоцк–Вентспилс
Приблизительно 12 лет тому назад произошла остановка настоящего трубопровода по причине снижения объема поставок нефти из России. Сложилась ситуация, когда труба нефтепровода была на протяжении почти 10 лет по всему своему объему заполнена стоящей нефтью.
Прекращение эксплуатации, однако, ни в коем случае не освобождает оператора от обязанности выполнять регулярное техническое обслуживание в целях обеспечения безопасности и функциональности трубопровода. Таким образом, в период с 2010 по 2013 г. компания CEPS выполнила опорожнение, химическую очистку и консервацию участка трубопровода протяженностью 250 км, проходящего от латвийско-литовской границы в Вентспилс.
Осенью 2012 года руководство компании ЛатРосТранс (владелец трубопровода) решило изучить возможность повторной проверки (комплексной проверки целостности) данного трубопровода высокого давления с целью его возможной будущей эксплуатации. Комплексная оценка проводилась на участке ранее химически очищенного трубопровода «3 79.км–НПС Джуксте» протяженностью примерно 8 км. Выполненная ревалидация включала следующие основные шаги:
- испытания материалов образцов трубы и модельное испытание целостности трубного тела,
- анализ результатов испытаний материалов,
- инспекция в режиме off-line с помощью магнитного диагностического снаряда TFI продвигаемого по трубе с использованием воды,
- анализ результатов внутритрубной инспекции,
- разработка программы необходимых ремонтов и испытания на целостность,
- выполнение программы ремонтов,
- испытание на прочность и герметичность (integrity test),
- осушка,
- инертизация.
Все указанные выше мероприятия были реализованы в течение 2013 года. Генеральным подрядчиком работ являлась компания CEPS, выполнение всех сварочно-монтажных и земляных работ обеспечила компания ЛатРосТранс.
Технические параметры трубопровода
Нефтепровод был построен в конце шестидесятых годов прошлого века. В отношении использованного трубного материала, к сожалению, не сохранились со времен строительства никакие сертификаты контроля, однако, в соответствии с информацией полученной от эксплуатационника, трубопровод изготовлен из продольно сварных труб 720 × 7 до 10,2 мм, произведенных в соответствии с ГОСТ 10704-63 (стандарт для производства продольно сварных труб) из стали типа 17ГС по ГОСТ 5058-65 (стандарт для производства горячекатаных листов из углеродистой стали).
Трубопровод был спроектирован для максимального давления 64 бар. Перед вводом в эксплуатацию на трубопроводе было в 1968 году выполнено гидроиспытание при давлении 60 бар, в 1990 году проводили повторное испытание при давлении 56 бар.
Для выполнения повторной проверки (ревалидации) был выбран участок трубопровода между населенным пунктом Петери (прим. 379 км) и НПС Джуксте протяженностью около 8 км. Высота местности по трассе трубопровода колебалась от 34 до 61 метров над уровнем моря. Трубопровод по всей своей длине проходим очистными поршнями и диагностическими снарядами.
Испытания материалов и модельные испытания трубного тела
Из участка «379 км – Джуксте» трубопровода Ду 700 был вырезан образец трубы длиной 8 м, состоящий из двух продольношовных сварных труб, соединенных монтажным кольцевым швом. Из указанного трубного образца были вырезаны три образца, длиной 3 × 1 м для испытания свойств материала. Из оставшейся части трубного образца был произведен тестовый сосуд, предназначенный для проведения модельного гидравлического испытания на прочность и герметичность, циклического нагружения и опрессовки до предела прочности, т.е. до разрушения.
Основной химический состав, механические и металлургические свойства трубного материала экспериментальным путем определил институт исследования материалов, АО СВУМ (SVÚM, a.s.). Анализ механических свойств и характеристик трещиностойкости, включая изучение кинетики роста усталостных трещин и определение порогового и критического размера трещины выполнены в испытательных станциях компании CEPS и UTAM AV ČR (Институт теоретической и прикладной механики Академии Наук Чешской Республики). Модельное гидравлическое испытание тестового сосуда на прочность и герметичность, циклическое нагружение и опрессовка до разрушения проводились опять в собственной испытательной лаборатории компании CEPS в сотрудничестве с компанией ООО «ADA Akustická emise, s.r.o.», которая в рамках выполняемых гидравлических испытаний проводила измерение при помощи датчиков акустической эмиссии (АЭ).
Испытания материалов
Согласно стандарту ГОСТ 5058-65, а также согласно стандарту ГОСТ 5520-79 свойства стали 17ГС должны соответствовать как минимум параметрам, приведенным в следующей таблице 1.
Re [МПа] | Rm [МПа] | A [%] | KCV при 0 °C [Дж/cm²] | KCU при –40°C [Дж/cm²] |
---|---|---|---|---|
мин. 345 МПа | мин. 510 МПа | мин. 23 % | мин. 34 | мин. 44 |
По результатам выполненных испытаний следует, что материал поставленной трубы соответствует требованиям указанных стандартов за исключением требования к ударной вязкости при −40 °C – см. таблица 2. В реальной практике, однако, у подземных линий такие экстремальные температуры обычно не встречаются даже в условиях латвийской зимы. По этой причине, значение ударной вязкости при отрицательных температурах для стальных труб, которые поставляются в соответствии с EN ISO 3183 или ранее действующим стандартом EN 10 208-2 как правило не приводятся, т.е. не требуются.
Место взятия образца, направление |
Rp0,2 [МПа] | Rt0,5 [МПа] | Rm [МПа] | A [%] | Z [%] | KCV при 0 °C [Дж/cm²] | KCV при –40°C [Дж/cm²] |
---|---|---|---|---|---|---|---|
Окружное направление | 375 | 417 | 561 | 26,60 | 50,64 | 56 | 17 |
Продольное направление | 373 | 389 | 560 | 28,07 | 56,82 | 79 | 18 |
Металл сварного шва | – | – | – | – | – | 52 | 25 |
Зона термического влияния | – | – | – | – | – | 64 | 17 |
На основании последующих испытаний механических свойств и трещиностойкости выявлено, что основной материал трубы обладает хорошей способностью блокировать развитие острых дефектов типа трещин.
Подготовка тестового сосуда, объем испытаний
части трубного образца был изготовлен тестовый сосуд, на котором постепенно выполнены следующие испытания и измерения:
- неразрушающая дефектоскопия (NDT) сварных швов,
- ориентировочное измерение толщины стенки трубопровода и твердости металла,
- модельное гидравлическое испытание на прочность и герметичность (integrity test),
- циклические испытания в целях проверки усталостной устойчивости,
- опрессовка до разрушения.
Секция трубопровода была с обоих концов заглушена и оборудована приварышами, оснащенными арматурами, к которым подключили шланги высокого давления для подачи и слива напорной воды и электронные датчики давления. К трубному образцу были затем прикреплены датчики акустической эмиссии (АЭ) – см. рис. 2.
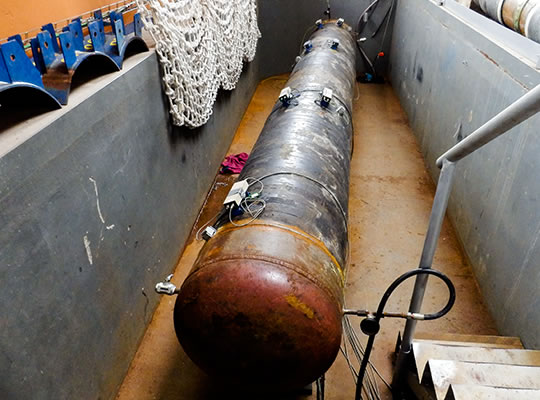
Рис. 2 – Тестовый сосуд
Модельное испытание тестового сосуда на целостность
Модельное испытание на целостность, т.е. контролируемая перегрузка тела трубы давлением до уровня предела текучести, проводилось в соответствии с технологической схемой «CEPS 98 Гидростатические испытания трубопроводов на прочность и герметичность (тнз. испытание на целостность, integrity test), включая стабилизацию дефектов».
Настоящее испытание на целостность (integrity test) представляет собой специально модифицированное гидростатическое испытание, основанное на чешском техническом стандарте TPG 702 04 и немецкой норме VdTÜV – Merkblatt 1060, в рамках которого при помощи повышенного давления воды в трубопроводе вызвано в стенке трубы напряжение близкое интегральному пределу текучести. Определение значения данного давления является одним из важнейших этапов подготовительных работ, поскольку:
- в случае низкого давления благоприятный эффект испытания на целостность вовсе не проявится,
- чрезмерно высокое давление вызывает негативное воздействие на материал и приводит к ухудшению состояния трубопровода и изоляции.
Параметры данного испытания на целостность были определены на основе результатов проведенных испытаний свойств материала.
Весь процесс нагрузки давлением проводился при одновременном непрерывном измерении AЭ. Установка датчиков AЭ с применением метода плоскостной локализации позволила точное определение источников акустических событий, т.е. точек развития микродефектов в теле трубы.
В течение модельного испытания на целостность проводилось при помощи чувствительных приборов требуемой точности и компьютеров on-line измерение, оценка и автоматическая регистрация следующих параметров:
- давление в тестовом сосуде,
- расход подкачиваемой воды,
- зависимость p–V (зависимость давления от подкачиваемого объема воды),
- зависимость нарастания давления от подкачиваемого объема воды ∆V/∆p,
- зависимость p–t (запись давления во времени),
- значение подкачанного объема воды для пластической деформации ΔVplast,
- значение интегральный окружной пластической деформации ε,
- поведение микрообъемов материалов с использованием акустической эмиссии, реагирующей на развитие микродефектов материалов.
В ходе испытаний на целостность (integrity test) было при помощи акустической эмиссии зарегистрировано 13 событий эмиссии. Подавляющее большинство данных событий эмиссии было зарегистрировано лишь в течение первого цикла испытания. Следовательно, акустическая эмиссия получила выражение стандартного эффекта Kaisera, что свидетельствует об устранении внутренних напряжений и стабилизации дефектов в материале трубы.
Циклические испытания тестового сосуда
После выполнения испытания на целостность (integrity test) была проверена стойкость к развитию в трубе усталостных дефектов, таких как трещины, и, соответственно, срок, на который можно с помощью испытаний на целостность продлить время службы трубопровода. Образец был подвержен циклическому усталостному нагружению при давлении в диапазоне примерно от 9,3 до 56,7 бар.
В ходе циклического нагружения проводились при помощи измерительных приборов и компьютера в on-line режиме измерения, оценка и автоматическая регистрация следующих параметров:
- давление в тестовом сосуде,
- регистрация давления во времени (контроль числа и величины испытательных циклов нагружения) – см. рис. 3,
- динамика изменения сигнала акустической эмиссии в ходе испытаний (проверка возможного развития усталостных трещин).
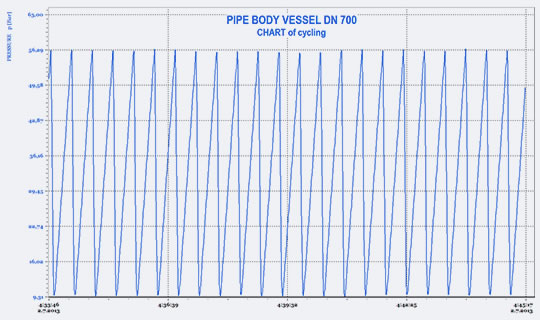
Рис. 3 – часть записи давления во времени в ходе циклических испытаний
Тестовый сосуд в течение 7 дней подвергли 16194 циклам, что с учетом частоты 1 цикл/1 день симулирует более чем 40 лет дальнейшей службы трубопровода. В ходе циклического нагружения образца не был выявлен никакой источник акустической эмиссии, имеющий признаки усталостного разрушения материала. Циклические испытания, выполненные после модельного испытания тестового сосуда на целостность, полностью подтвердили повышенную стойкость трубного образца к возможному развитию усталостных дефектов.
Опрессовка до разрушения
Опрессовка до разрушения осуществлялась монотонным нагружением без задержек подкачки воды. Разрушение трубного материала произошло при давлении 101,45 бар. Данное давление было примерно на 1,5 бар ниже теоретического давления предела прочности.
Причиной разрушения было нарушение целостности материала трубы в переходной зоне заводского продольного сварного шва, откуда образовавшаяся трещина мгновенно распространилась по оси трубопровода в обоих направлениях и остановилась только после перехода в основной материал трубы – см. рис. 4.
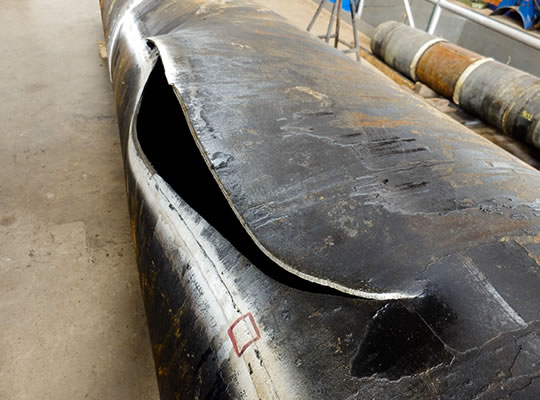
Рис. 4 – Тестовый сосуд Ду 700 после разрушения
Оценка испытаний материала и модельных испытаний
Выполненные испытания материалов показали высокое качество стального материала труб, и доказали, что его свойства (помимо упомянутого выше несоблюдения стандартных значений ударной вязкости при −40 °C) более чем соответствуют требованиям стандарта ГОСТ 5520-79, а также, после более чем сорокалетнего периода эксплуатации не было выявлено никаких признаков деградации материала трубы.
Из результатов испытания на целостность и измерений акустической эмиссии следует, что в течение контролируемой опрессовки трубного образца до предела текучести произошло снижение внутренних напряжений и стабилизация дефектов в материале трубы. Впоследствии, во время циклических испытаний не было в образце трубы при помощи акустической эмиссии обнаружено развитие каких-либо опасных дефектов, даже при весьма суровой симуляции долговременной эксплуатации путем циклического нагружения внутренним давлением.
Основываясь на результатах экспериментального исследования свойств материала трубы и их анализа, можно сделать вывод, что труба пригодна для испытания на целостность, и, соответственно, вполне реалистично ожидать, что после его выполнения трубопровод можно будет безопасно и надежно использовать в качестве газопровода или же продуктовода.
Внутритрубная инспекция трубопровода
Как известно, на трубах почти всегда встречаются производственные дефекты, которые не были выявлены в рамках выходного контроля качества готовой продукции, а также дефекты сборки труб (сварка, укладка), дефекты вызванные рабочей нагрузкой, коррозионные дефекты, и дефекты, вызванные третьими лицами. По данной причине, выбранный участок подвержен внутритрубной инспекции, основной целью которой обнаружение и локализация дефектов, которые бы, несомненно, не выдержали давление во время последующего испытания на целостность.
На трубе нефтепровода Ду 700 «Полоцк–Вентспилс» была в последний раз проведена внутритрубная инспекция с использованием магнитного поршня-дефектоскопа типа MFL и ультразвукового поршня типа UT в 2000 году. Вскоре после выполнения инспекции была перекачка нефти по трубопроводу остановлена. Давление в трубопроводе было сведено к минимуму, т.е. давление зависело лишь от гидравлического давления и теплового расширения нефти. По данной причине, на данный момент уже не предполагается дальнейшее развитие усталостных дефектов (в частности образование и рост трещин в стенке трубы), вызванных перепадами рабочего давления в трубопроводе. Однако, несмотря на непрерывную работу катодной защиты, нельзя на протяжении последних 13 лет исключить развитие дефектов, вызванных коррозией. По приведенной причине, оператор трубопровода принял решение осуществить до выполнения испытания на целостность (integrity test) внутритрубную инспекцию в режиме off-line с применением дефектоскопа поперечного намагничивания типа TFI.
Поскольку испытываемый участок трубопровода не оборудован камерами пуска-приема ни интеллигентных снарядов-дефектоскопов, ни очистных поршней, компания CEPS заблаговременно обеспечила проект и производство временных камер и мобильных адаптеров для выполнения, на данный момент еще вовсе не привычной, инспекции в режиме off-line – см. рис. 5.
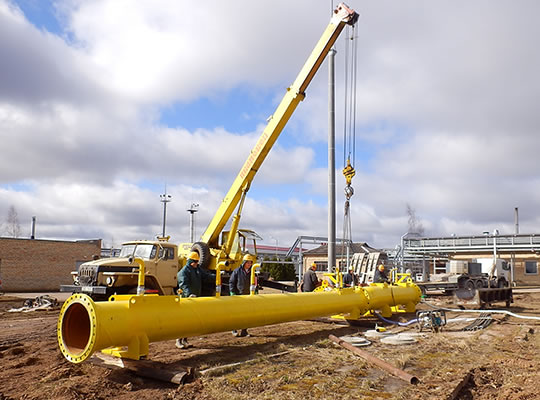
Рис. 5 – Мобильные адаптеры для инспекционных снарядов-дефектоскопов
Поскольку труба нефтепровода осталась после химической очистки и последующей консервации пустой, пришлось обеспечить постоянное продвижение дефектоскопа по трубопроводу с помощью альтернативной среды. В данном случае в качестве альтернативной среды применили воду, которая в достаточных количествах находилась на территории нефтеперекачивающей станции. Пропуск дефектоскопа по трубопроводу с помощью подкачиваемой воды обеспечила компания CEPS в сотрудничестве с компанией LatRosTrans.
Пропуск снаряда-дефектоскопа
Пропуск снаряда-дефектоскопа поперечного намагничивания типа TFI по трубопроводу осуществлялся с использованием воды, подкачиваемой из временных резервуаров, расположенных на территории перекачивающей станции Джуксте. Исходя из требований подрядчика внутритрубной инспекции, снаряд-дефектоскоп поперечного намагничивания TFI пропускался по трубопроводу со скоростью не менее 0,5 м/с, см. рис. 6, что соответствует скорости подачи не менее чем примерно 190 л/с, т.е. около 685 м³/ч воды в трубопровод. Всего было в течение примерно 4,5 часа закачано 3100 м³ воды, что соответствует общему геометрическому объему инспектируемого трубопровода. После пропуска снаряда-дефектоскопа TFI по трубопроводу, отработанная вода была вытеснена из трубопровода и слита обратно в резервуары. В качестве иллюстрации можно привести, что такой объем хватит для питания всех фонтанов в садах Версаля в течение целого часа.
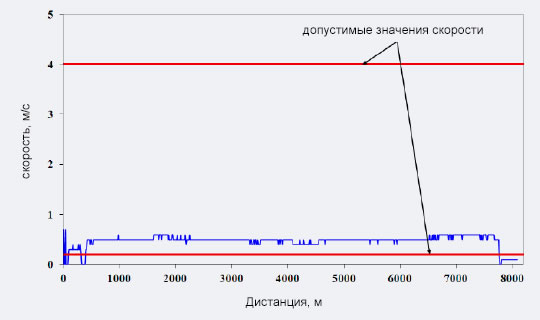
Рис. 6 – Скорость движения дефектоскопа типа TFI по трубопроводу
В целях обеспечения поставки такого огромного количества воды в течение нескольких часов, было необходимо между резервуарами и концом трубопровода Ду 700 построить четыре временных водопроводных линии (1 × Ду 200 и 3 × Ду 100), соединяющие конец трубы инспектируемого участка с мобильными насосами, расположенными вблизи резервуаров – см. рис. 7.
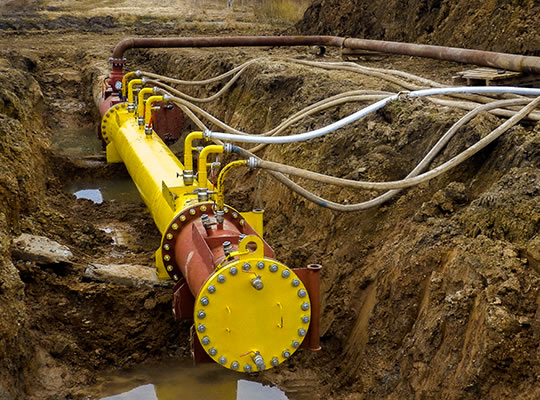
Рис. 7 – Подключение системы камеры-пуска и адаптеров к водопроводной линии
После приема и изъятия снаряда-дефектоскопа из наконечника камеры приема, была выполнена проверка полученных данных, которая подтвердила, что снаряд-дефектоскоп TFI продвигался уже во время первого пропуска по трубопроводу с требуемой скоростью, и, следовательно, измеренные данные пригодны для дальнейшей обработки.
Анализ результатов дигностическкого обследования
После выполнения внутритрубной инспекции измеренные данные были анализированы.
Список дефектов, устранение которых на основе анализа рекомендуется, основывается на требовании обеспечить безопасность будущей эксплуатации трубопровода. В рамках внутритрубной инспекции были в стенке трубы выявлены аномалии, которые были затем проанализированы и оценены. На основе know-how подрядчика внутритрубной инспекции и типа использованного дефектоскопа, выявленные аномалии оценены как дефекты определенного типа и размера. Данные дефекты затем различными аналитическими методами анализировались с точки зрения прочности. В рамках данных расчетов, отсутствующая информация о фактической форме и размере каждого дефекта корректируется с помощью ряда коэффициентов. На основе последующих расчетов прочности и установленных критериев, рекомендуется устранить те дефекты, которые теоретически не соответствуют выдвинутым требованиям к прочности. Объем дефектов, устранение которых рекомендуется, всегда зависит от типа примененного аналитического метода оценки. Прочностные расчеты всех дефектов были рассчитаны для давления 32,6 бара, что соответствует максимальному рабочему давлению трубопровода в прошлом.
Исходя из выполненного анализа, подрядчик внутритрубной инспекции рекомендовал реализовать в течение 1 года ремонт 11 дефектов, в течение двух лет ремонт 1 дефекта, и в течение 10 лет ремонт 22 дефектов, и десятки других дефектов отремонтировать в рамках капитального ремонта. В течение первого года было рекомендовано преимущественно отремонтировать вмятины, которые потенциально могут содержать другие дефекты, а в течение десяти лет (помимо вмятин) также некоторые коррозионные дефекты.
Принцип испытания целостности (integrity test)
Испытание целостности (integrity test) представляет собой специально модифицированное испытание на прочность долговременно эксплуатируемых стальных трубопроводов, которое проверит истинный интегральный предел текучести трубопровода, и, следовательно, его безопасность в условиях рабочего давления. Принцип данного испытания заключается в нагружении трубопровода высоким давлением воды до уровня, близкого интегральному пределу текучести, т.е. сверхдавление воды вызывает в стенке трубы напряжение близкое пределу текучести.
Локальные точки с внутренним напряжением будут переведены в состояние пластичности, сопровождаемое упрочнением материала, который во время следующей нагрузки ведет себя как упругий. Происходит, конечно, использование определенной части запаса пластичности материала, однако, такое использование части запаса пластичности материала является минимальным, и в рамках испытания на целостность его учитывают.
Испытание на целостность приводит к положительному воздействию на следующие характеристики трубы и материала:
- снижение и перераспределение внутренних напряжений, порожденных в стенке трубы в процессе производства,
- снижение и перераспределение внутренних напряжений, порожденных в течение укладки трубопровода,
- перераспределение пиков напряжения в местах концентраторов напряжений-надрезов (дефектов),
- уменьшение пиков напряжения в больших областях стенки (например, сварной шов и околошовная зона, овальность, деформации) и устранение образования коррозионного растрескивания под напряжением и развития усталостных трещин,
- перераспределение неблагоприятных концентраторов напряжений у дефектов, таких как питтинговое или сплошное коррозионное разъедание,
- блокировка развития острых докритических дефектов, способных дальнейшего роста (типа трещины) путем создания пластической зоны на вершине и образованием напряжения при сжатии в данной области после разгрузки,
- частичная блокировка роста трещин докритического размера характера коррозии под напряжением, которые иначе сложно прослеживаются,
- идентификация дефектов критического размера. Благодаря тому, что давление создается с помощью воды, раскрытие безопасно, и точку дефекта можно относительно легко обнаружить, вырезать и заменить новой трубой.
Результат выполненного испытания на целостность (integrity test), таким образом, помимо проверки фактического технического состояния трубопровода, создает, в частности, условия для его безопасной эксплуатации путем устранения явных дефектов в трубе и долгосрочной блокировки (стабилизации) дальнейшего развития других дефектов в стенке трубы в следствие усталостных процессов.
Ревалидация дефектов и рекомендаций, вытекающих из внутритрубной инспекции, с учетом последующего испытания трубопровода на целостность
В рамках ревалидации (повторной оценки) трубы намеренно использовали комбинацию внутритрубной инспекции и последующего испытания на целостность путем выдержки под давлением. Это позволяет принципиально иной подход к результатам внутритрубной инспекции. Дефекты, выявленные в рамках инспекции, таким образом, делятся на две основные группы:
- крупные дефекты (сверхкритические), которые бы в рамках испытания на целостность, очевидно, раскрылись. Данные дефекты подлежат ремонту путем вырезки,
- дефекты менее крупные (докритические), которые бы в случае простой внутритрубной инспекции подлежали ремонту, но при перегрузке давлением в рамках испытания на целостность произойдет их стабилизация, и, следовательно, в их ремонте нет необходимости.
Данный подход значительно снижает количество необходимых ремонтов трубопровода после инспекции, и обеспечивает значительно более высокий уровень окончательной надежности трубопровода, поскольку в ходе испытания на целостность происходит стабилизиция и других дефектов, которые не были в пределах выполненной инспекции предназначены для ремонта, или даже не были вовсе выявлены. Такие недостаточно выявленные или оцененные дефекты могут в ходе испытания на целостность оказаться даже сверхкритическими и раскрыться.
В оценке дефектов, выявленных и стандартно оцененных подрядчиком внутритрубной инспекции, применен следующий подход:
- повреждения типа вмятин, расслоений, и сварных дефектов не были ремонтированы – прочность труб в данном месте проверена в течение испытания на целостность. Предполагалось, что в течение испытания на целостность произойдет в данных местах перераспределение пиков напряжения в точках концентраторов напряжений-надрезов. Данная теория была проверена, напр., уже в рамках модельного испытания тестового образца на целостность, где кольцевой сварной шов был оценен как неудовлетворительный из-за отсутствия корневого слоя. При выполнении испытания на целостность, произошла, на основе информации акустической эмиссии, стабилизация данных дефектов в корневом слое кольцевого шва. Кроме того, разрушение тела трубы произошло в зоне термического влияния продольного сварного шва, где не было найдено никаких дефектов,
- дефекты типа потери металла рассчитывались аналитическими методами:
- B31.G (ASME),
- Modified B31.G (ASME) и RSTRENG,
- DNV Code.
- Критерием оценки каждого дефекта данного типа была его удовлетворительность с точки зрения нагрузки при предполагаемом максимальном давлении в рамках испытания на целостность (в данном случае на уровне 75 бар).
- дефекты типа недопустимых ремонтных конструкций, а также дефекты временно устраненные в ходе эксплуатации, были отнесены в категорию дефектов, подлежащих безоговорочному ремонту. Это касается временных ремонтов (заделка наглухо) недопустимых засверловок, заплат и устранения вантузов.
Если оценивать выше приведенные методы с точки зрения консерватизма, то, общеизвестно, критерий B31.G является надежным, но на практике несколько консервативным. С целью уменьшения степени консерватизма, впоследствии были разработаны и апробированы критерии Modified B31.G и RSTRENG. Критерий DNV Code (RP-F 101) по сравнению с методом B31.G менее консервативен с точки зрения всех размеров сплошного повреждения.
За основу для выбора подлежащих ремонту дефектов с потерей металла мы взяли оценку дефектов по методу Modified B31.G и RSTRENG с учетом оценки дефектов по методу DNV Code. Все дефекты, которые бы в течение испытания на целостность достигли теоретического (расчетного) максимального нагружения, т.е. разрушения, были предназначены для ремонта.
Все сварочно-монтажные, земляные и изоляционные работы, реализованные в соответствии с программой ремонта, выполнила компания ЛатРосТранс.
Реализация программы ремонта дефектов
В отличие от всех предыдущих ремонтов, выполняемых на трубопроводе в прошлом, в этот раз все сварочно-монтажные работы (сварка, газовая резка и шлифовка) проводились в постоянно безопасной среде без каких-либо, в других случаях необходимых, мер безопасности направленных на обеспечение взрывобезопасной среды. По данной причине, не устанавливали никакие муфты или заплаты, а из трубопровода в данных зонах вырезали участки длиной не менее 1 м и воссоединили исправной трубой.
Незначительные дефекты типа засверловок были перекрыты с помощью приварышей (фитингов) TDW TOR 2″, Ру 100. Затем с применением сверлильного механизма TDW стенку трубы просверлили. Это позволило удалить возможные надрезы в стенке трубы, обеспечивая при этом одновременно, что область фитинга после испытания на целостность можно было не только опорожнить, но и просушить.
Разрушение в ходе испытания на целостность
Перед проведением гидравлических испытаний трубопровод был разделен примерно в половине на два участка.
В ходе регулируемого увеличения давления произошло на участке № 1 при давлении 70,5 бар разрушение трубы. В рамках данного разрушения снизилось давление в трубопроводе в течение 1 секунды до 0 бар, что соответствует утечке примерно 10 м³ воды. Исходя из данного факта, было выдвинуто предположение, что точка разрушения будет найдена простым осмотром трассы трубопровода. Данное предположение полностью оправдалось, тогда как место разрушения было локализовано в пределах одного часа. Как показано на рис. 8, данная массивная утечка воды не представляла опасность для окружающей среды,однако защита трассы трубопровода с целью предупреждения доступа посторонних лиц и попадания механизмов в течение гидравлических испытаний была необходимой.
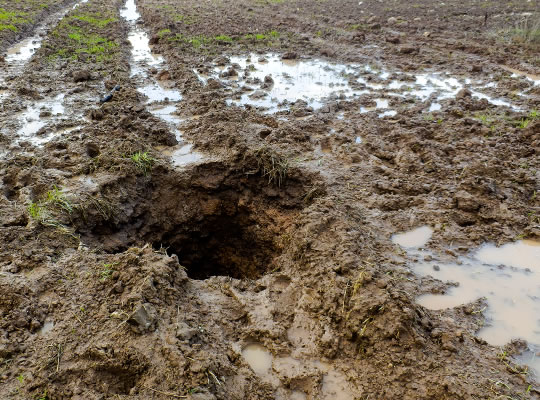
Рис. 8 - Место разрушения
Причиной разрушения являлась продольная трещина в середине продольного заводского шва на внешней стороне трубы в положении «12 часов» – см. рис. 9. Поперечные (окружные) разрезы на трубе были произведены лишь впоследствии в рамках сварочно-монтажных работ, связанных с временным ремонтом поврежденного участка, поскольку из участка следовало до выполнения окончательного ремонта вытеснить примерно 1700 м³ воды.
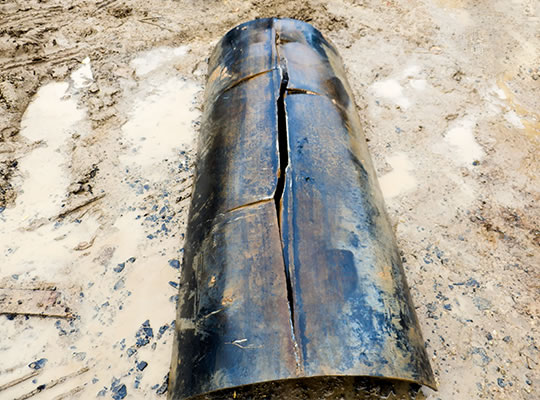
Рис. 9 – Поврежденная труба в точке разрушения
У поврежденного продольного сварного шва был на внешней поверхности излома выявлен черный слой – см. рис. 10. Данный слой, в самой глубокой точке, проходил до глубины 7 мм, тогда как общая толщина стенки трубы в месте дефекта, т.е. область продольного сварного шва, составляла примерно 11 мм. Длина данной зоны при наружной поверхности с несплошным черным покрытием составляла около 150 мм, однако общая длина трещины достигала вплоть до 250 мм.
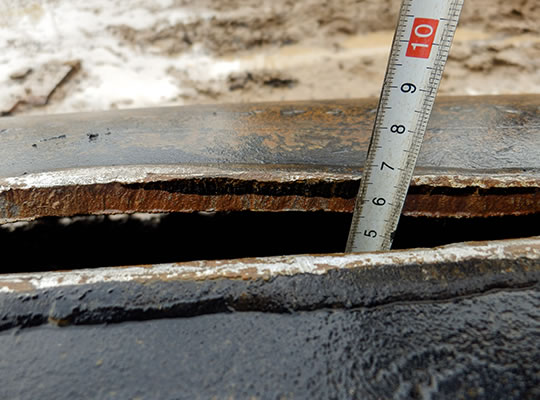
Рис. 10 – стенка трубы в точке дефекта
В ходе обследования было выявлено, что черное покрытие на стенке поверхности разрушения являлось стандартно применяемым изоляционным битумным праймером. В рамках выполнения заводского изоляционного покрытия, использованная разогретая битумная масса, вероятно, частично проникла в поверхностные трещины продольного шва. Интенсивность покрытия поверхности трещины битумным материалом, конечно, зависит от степени ее раскрытия. Тем самым можно объяснить, почему поверхностная трещина не была загрязнена битумным праймером по всей своей длине.
Приведенные выше результаты наглядно показали, что данная продольная трещина образовалась еще в процессе производства, присутствовала в трубе на протяжении более 40 лет и не была выявлена никакими общедоступными методами внутритрубной инспекции, которые в течение последних 13 лет проводились.
Настоящий случай еще раз подтверждает многолетний опыт компании CEPS, заключающийся в том, что чрезвычайно опасные дефекты данных размеров, а именно трещины в продольном направлении трубы, в настоящее время с помощью инспекционных снарядов-дефектоскопов весьма сложно выявляемы.
В данном контексте важно отметить, что дефекты, которые после стандартной оценки внутритрубной инспекции рекомендовалось устранить, но которые после выполнения прочностных расчетов не были отремонтированы, тем не менее, выдержали давление 72 бар в течение 24 часов, т.е. давление примерно в два раза превышающее значение, для которого велся первоначальный расчет. Наоборот, разрушение продольного сварного шва произошло в месте, где ни TFI, ни Ultrasonic, ни MFL дефектоскоп в 2001 году никаких аномалий не обнаружили, хотя трещина указанного размера в сварном шве уже во время выполнения инспекций совершенно очевидно находилась.
После выполненного ремонта, участок № 1 подвергли повторному испытанию на целостность.
На основании испытания на целостность (стресстест, испытание на прочность и герметичность) была труба участка № 1 признана прочной и герметичной. Затем, гидравлические испытания проводили таким же образом и на втором участке, который также был оценен как прочный и герметичный.
После гидравлических испытаний был трубопровод просушен до температуры точки росы (ТТР) −20 °C и снова опресссован инертной смесью на основе азота.
Пример из Польши
В 2010 году компания CEPS проводила испытание на целостность в Польше, на трубопроводе высокого давления длиной 56 км. Трубопровод был построен в 1997 году из спирально-шовных труб 406 × 6,3 мм из стали типа 18G2A. Перед гидравлическими испытаниями проводилась внутритрубная инспекция с помощью снаряда-дефектоскопа типа MFL. На основании данной внутритрубной инспекции были все дефекты, оцененные подрядчиком внутритрубной инспекции как критические, отремонтированы. В ходе первого цикла испытания на целостность была на одном из испытываемых участков зарегистрирована значительная утечка.
После локализации и откопки места утечки воды, был в положении «12 часов» найден впечатляющий кольцевой монтажный сварной шов – см. рис. 11, причем было очевидно, что на материале облицовочного слоя сварщик явно не экономил. Однако, корень в точке перфорации искать было напрасно. Удивительно, что такой шов, на котором с первого взгляда явны существенные недостатки, прошел всеми проверками, которые должны были быть выполнены во время строительства.
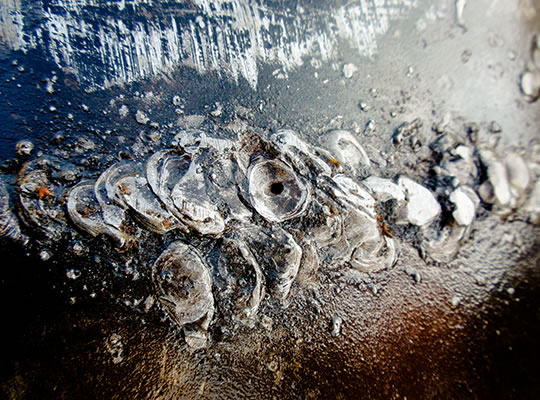
Рис. 11 – Сквозной дефект сварного монтажного шва
В рамках повторной проверки результатов внутритрубной инспекции данного места не были найдены в записи интеллигентного инспекционного снаряда-дефектоскопа никакие аномалии.
Ревалидация продуктоводов в Чешской Республике
Компания CEPS за последние 10 лет выполнила на территории Чешской Республики испытания на целостность после внутритрубной инспекции с помощью снаряда-дефектоскопа типа MFL на более чем 200 км продуктоводов. В ходе данных испытаний было обнаружено более 20 дефектов, которые имели сквозной характер уже в ходе проведения внутритрубной инспекции или были причиной разрушения трубопроводов во время гидравлических испытаний. Во всех именуемых случаях, данные критические дефекты не только не были расценены как дефекты подлежащие ремонту, но, довольно часто, не были вовсе интеллигентным инспекционным снарядом-дефектоскопом обнаружены.