Oil removal and DN 700 pipeline cleaning in Latvia
Hundred kilometres long part of crude oil pipeline DN 700 Polock–Ventspils in Latvian territory was drained in December 2010. Chemical cleaning of this pipeline section by a special chemical cleaning agent PETROSOL was finished in June 2011. Then the section was filled by nitrogen. The result of these activities was that environmental pollution risk due to oil leakage was eliminated and the section is decommissioned and prepared for the next possible use in the future.
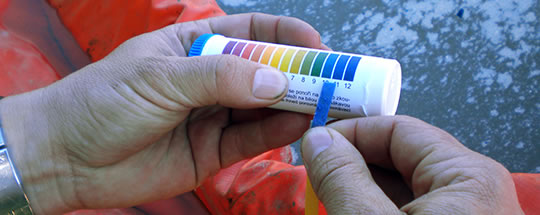
Crude oil pipeline DN 700 Polock–Ventspils is northern part of Druzhba pipeline which in the past supplied crude oil especially to the former Soviet Union and central European countries.
Nine years ago oil supplies to Latvia and Lithuania were stopped due to economic and political reasons and the pipeline containing approx. 1.9 million barrels of crude oil remained shut down and blocked for any other use. This fact did not relieve the operator from the obligation and responsibility to do regular maintenance and to ensure its safety, security and functionality.
For that reason, in 2010 the pipeline owner, decided to decommission this pipeline. Draining, decontamination and inertization by nitrogen was done on Latvian territory between Lithuanian border and Ventspils oil terminal including 3 loopings located on Musa river crossing, at Džūkste pump station output and at Ventspils´ nature reserve wetlands.
Czech pipeline servicing company CEPS a.s. won the tender and was awarded a contract in early October 2010. The design and technical preparation was carried out during the following two months so emptying of the first pipeline part could begin in late November 2010.
Preparation
Before starting the work the pipeline was divided in 6 sections for technical reasons. LatRosTrans divided the pipeline using line plugging technology and performed excavation as well as welding and assembly work. Temporary traps supplied by CEPS were welded at the end of each section – see figure 1.
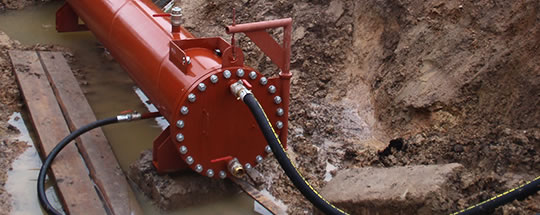
Figure 1 – Special temporary trap
Displacement of crude oil from the pipeline
Two batching pigs were inserted into each launching trap. Water was pumped into the space between the pigs and inert water batch was pushed steadily through the pipeline.
Crude oil was displaced this way directly into an existing stable 50,000 cubic meters tank at the oil terminal in Ventspils. Before that, the crude oil from the loopings was pushed through interconnecting pipeline to the main line the same way.
Pipeline decontamination
Decontamination of the emptied pipeline was done by chemical cleaning. The main objective was to achieve clean internal surface of the pipeline so that contamination of soil and underground water would not be possible in case of pipe wall penetration by corrosion or by some other reason in the future. The works on the pipeline between “Latvian border and pump station Džūkste“ started in early May 2011. At the beginning special launching and receiving traps were installed on each end of the sections to be cleaned – see figure 2 and figure 3.
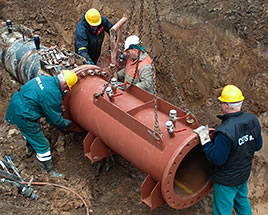
Figure 2 – Installation of special launching and receiving trap
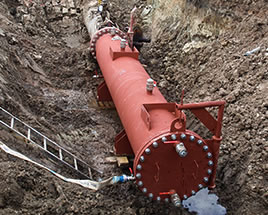
Figure 3 – Installed trap
Several batching pigs were inserted into each launching trap. Different decontamination batches containing water solution of PETROSOL cleaning agent in specified concentrations and volumes were prepared and ran through the pipeline. After passing the cleaning train through the pipeline, the internal surface of the pipeline was completely clean without any trace of oil – see figure 4.
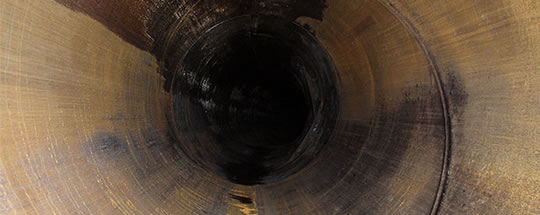
Figure 4 – Internal surface of pipe after decontamination
Every time the clean train arrived at the receiving trap, samples of water were taken from the last water-purging batch to check residual concentration of hydrocarbons in water (VOC) – see figure 5 and figure 6. The concentration of VOC allowed by local authorities was 30 mg/l.
The concentration in the samples measured in accredited laboratory never exceeded 1 milligram.
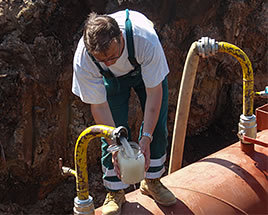
Figure 5 – Collection of water samples
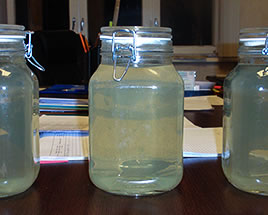
Figure 6 – Collected water samples
Treatment of waste water using biodegradation
All decontaminated and water-purging batches with a total volume of 1850 m³ were accumulated in temporary retention reservoirs, which had been built for this purpose by pipeline operator in the area inside Džūkste station – see figure 7.
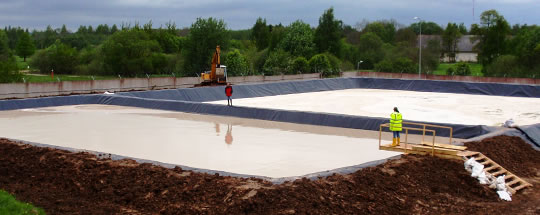
Figure 7 – Temporary retention reservoirs
In the retention reservoirs, the waste water solution containing hydrocarbons was chemically modified, thus hydrocarbon residues were partially separated from the water. After removing the oil floating on the surface, the dissolved hydrocarbon residues were removed using a biological degradation method – see figure 8. This method is based on the application of bacterial preparation which is introduced into the waste water to be treated. The biodegradation process of hydrocarbons decomposition is completed within several weeks. Higher temperatures and plenty of oxygen accelerate the process.
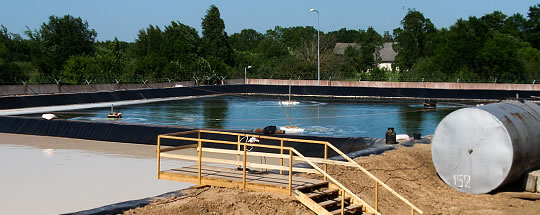
Figure 8 – Biological degradation of hydrocarbon residues
The cleaning traps were cut off at the end of decontamination and the sections were connected or sealed off by pressure cups. Thanks to the completely removal of hydrocarbon from the inside of the pipe, this created a permanent safety atmosphere for the assembly-welding activities without further necessary safety precautions against explosion – see figure 9.
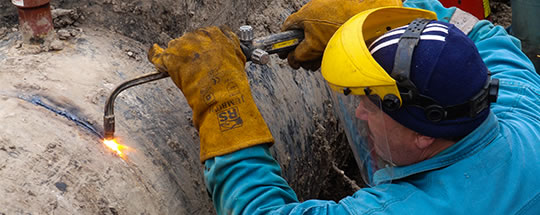
Figure 9 – Flame cut in permanent safety atmosphere
Pipeline conservation
The first step – passivation using trinatriumphosphate
At the end the cleaning train behind the last water-purging batch, the passivation batch – the water solution of trinatriumphosphate (Na₃PO₄) – was pumped in. The aim of the passivation process is to create corrosion resistible environment on the steel surface.
The controlled run of the batch through the pipeline creates thin passivating phosphate film on the inner surface of the pipes and in combination with high level of pH effectively shields the steel surface against further corrosion.
The second step – inertization of inner pipeline space by nitrogen
After the tie-in of all the decontaminated parts, the pipeline was purged by 95% nitrogen. The nitrogen source was a special mobile unit producing nitrogen by membrane separation of the air.
This unit fed by 14 bar compressed air was developed in cooperation of CEPS and specialized manufacturer of membrane separators. The entire unit is installed in one 20 feet ISO 1C container adapted for easy operation – see figure 10.
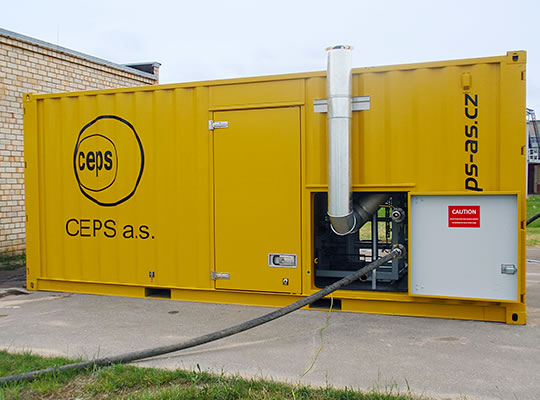
Figure 10 – Mobile nitrogen unit
The feeding compressed air is at the input of unit cleaned to remove dust and condensed water. The clean air is preheated and then continues into the membrane separator. As the permeability of nitrogen through the membrane is lower than in the case of oxygen, the nitrogen concentration in the stream of gas at the output of separator is substantially higher (95%) than in the atmosphere (79%). However, the air in the waste stream is enriched by oxygen up to the concentration 30% (compared with 21% in the atmosphere). The volume of produced inertization gas is about one half of the process air volume coming into the separation unit. The inertization gas was channelled into the pipeline by pressure hoses.
The pressure of nitrogen inertization mixture in the pipeline will be maintained at 3 bar, the level which is far lower than the design and operation pressure. In the case of any mechanical damage to the pipeline only the inertization gas escapes without any danger of pipeline rupture.